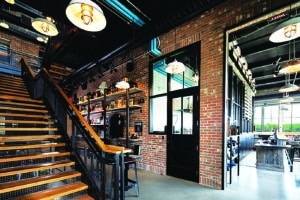
Great Marsh Brewing Co.’s new 13,000-square-foot location in Beverly includes a brewery, brewery, full kitchen, restaurant and bar, tap room and outdoor deck. Photo by Camille Maren | Courtesy
Already well-known as the birthplace of fried clams and home to several popular restaurants, the causeway in Essex seemed to John Collins the ideal spot for a new local brewery and restaurant. But achieving Collins’ vision on marshland in this scenic coastal town would require some creative construction. With 140 years of experience in water-adjacent construction, Connolly Brothers was hired on a design/build basis and responded with a friction pile foundation system that took into account the Essex River Basin’s ocean tides.
The result is the Great Marsh Brewing Co., which launched in November 2019 with an impressive 13,000-square-foot presence: a state-of-the-art brewery with a tap room, full kitchen, restaurant and bar and outdoor deck.
Great Marsh Brewing Co. got its start as a basement operation. Chief Executive Brewer John Collins contacted Connolly Brothers and realized that the design/build model would streamline the new venture while allowing more flexibility during design and construction.
Enlisted early on, Connolly was responsible for all aspects of Great Marsh’s completion, including site feasibility, early conceptual budgeting and design, to engineering, permitting and installing high-end brewery equipment from German manufacturer BrauKon.
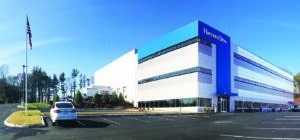
The Harmonic Drive headquarters in Beverly includes 97,000 square feet of office, assembly and high-bay manufacturing space. Photo courtesy of Harmonic Drive
A Homecoming for Harmonic Drive
When designing and building a new corporate headquarters for a company whose products help move Mars rovers, unique construction needs are to be expected. Harmonic Drive, which manufactures precision strain wave gears and components, was able to return to Beverly, where it was originally founded in 1960 as a division of the United Shoe Machine Corp.
The Harmonic project was completed on an accelerated schedule that featured pre-release of steel and structural materials. To meet Harmonic’s long-term vision, Connolly developed a plan that prioritized flexibility.
For instance, Harmonic Drive was interested in the ability to move their heavy and high-tech machines anywhere within the manufacturing facility, as well as the option to add new machines in the future without significant interruption to ongoing processes. Typically, such machines are placed into built-in floor footings and foundations designed for each specific piece of equipment. However, such an approach requires a rigid machine shop floor plan. To enable Harmonic to move current and future machines freely about the facility, Connolly placed a 12-inch thick concrete slab throughout the machine shop space.
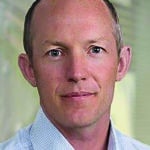
Thad Minshall
Now open, the new corporate campus for Harmonic Drive consists of 97,000 square feet –
split between a 3-story office building, assembly space, and a high-bay manufacturing space – on a previously undeveloped lot in Beverly’s Dunham Ridge Business Park. The site can also accommodate expansion.
Not long ago, design-build was the exception to the rule for how construction projects were delivered. The value of the process and the collaborative all-in-one-contract teams has been proven to the point that today, almost half of all building projects in the US are delivered using the design-build method.
Thad Minshall is vice president of real estate and development at Connolly Brothers, a general contractor and construction management firm based in Beverly.